Назначение основных элементов рулевого управления. Рулевое управление автомобиля. Общие принципы работы
19.03.2013 в 05:03
Это основной элемент системы рулевого управления, связывающий вал рулевого колеса и тягу рулевого привода.
Рулевой механизм выполняет следующие функции:
– увеличение усилия, прилагаемого к рулевому колесу;
– передача усилий рулевому приводу;
– возврат рулевого колеса в нейтральное положение, при снятии нагрузки и отсутствии сопротивления.
Рулевой механизм представляет собой механическую передачу, иначе говоря, редуктор. Основной параметр рулевого механизма – передаточное число, которое определяется отношением числа зубьев ведомой шестерни к числу зубьев ведущей.
Различают три типа рулевых механизмов системы рулевого управления в зависимости от типа механической передачи: реечный, червячный, винтовой.
1. Реечный рулевой механизм
Конструкция
Это самый распространенный тип рулевого механизма, устанавливаемого на легковые автомобили. Реечный рулевой механизм состоит из:
– шестерни, устанавливаемой на валу рулевого колеса;
– рулевой рейки зубчатого типа, соединяющейся с шестерней.
Реечный механизм конструктивно прост, имеет высокий КПД и высокую жесткость. Однако такой механизм чувствителен к ударным нагрузкам по причине дорожных неровностей и склонен к вибрациям. Данный тип механизма устанавливается на автомобилях, имеющих передний привод с независимой подвеской управляемых колес .
Принцип работы
1. С вращением рулевого колеса рулевая рейка перемещается влево и вправо.
2. С движением рулевой рейки происходит перемещение присоединенной к ней тяги рулевого привода и поворачивание колеса автомобиля.
2. Червячный рулевой механизм
Конструкция
Червячный механизм состоит из:
– глобоидного червяка (червяка с переменным диаметром);
– рулевого вала;
– ролика.
На валу ролика за корпусом рулевого механизма установлен рычаг (сошка), который связан с тягами рулевого привода.
Червячный механизм имеет меньшую чувствительность к ударным нагрузкам, обеспечивая большие углы поворота колес, результатом чего является лучшая маневренность автомобиля. Но червячный механизм сложен в изготовлении и его стоимость велика. Данному механизму требуется периодическая регулировка из-за большого числа соединений.
Червячный механизм используется на машинах повышенной проходимости с зависимой подвеской управляемых колес и легких грузовых автомобилях .
Принцип работы
1. С вращением рулевого колеса обеспечивается перемещение ролика по червяку (обкат), качание сошки.
2. Происходит перемещение тяги рулевого привода, благодаря чему колеса поворачиваются.
3. Винтовой рулевой механизм
Конструкция
В конструкцию винтового механизма входят:
– винт на валу рулевого колеса;
– гайка, которая перемещается по винту;
– зубчатая рейка, нарезанная на гайке;
– зубчатый сектор, который соединен с рейкой;
– рулевая сошка, расположенная на валу сектора.
Главная особенность винтового механизма – соединение винта и гайки производится с помощью шариков, что приводит к меньшему трению и износу пары.
Общее устройство и принцип работы системы рулевого управления автомобиля, как и многих других современных транспортных средств, можно описать следующим образом. Рулевое управление имеет рулевые тяги, рулевой механизм с реечной или червячной передачей и рулевую колонку, оканчивающуюся рулевым колесом. Функционирует система довольно просто: при воздействии на руль усилие через рулевой механизм передается на рулевые тяги, которые шарнирно связаны с рычагами подвески, что приводит к изменению траектории движения авто. Кроме того, рулевое колесо информирует водителя о состоянии дорожного покрытия, определяемое по величине усилия, приложенных к рулю. Если не брать во внимание размер рулевого колеса у спорткаров, диаметр руля для большинства автомобилей находится в пределах 38-42,5 см.
Рулевое колесо соединяется с рулевым механизмом посредством травмобезопасной рулевой колонки, которая имеет несколько карданных соединений. Травмобезопасность заключается в том, что при лобовом столкновении на большой скорости она (колонка) складывается, снижая таким образом степень тяжести нанесенных водителю травм. Современные автомобили снабжены электрической или механической регулировкой адаптации рулевой колонки под рост водителя. Изменение осуществляется как в вертикальном направлении, так и по длине, либо в двух направлениях. Также предусмотрена противоугонная защита путем блокирования рулевой колонки электрическим или механическим способом.
Рулевой механизм выполняет роль множителя усилий, приложенных водителем к рулевому колесу с последующим распространением нагрузки на рулевой привод. Самым применяемым типом редуктора рулевого механизма в автомобилях является червячная и реечная его конструкции, причем первый вариант чаще использовался в автомобилях прошлого столетия. Реечный вариант представляет собой цилиндрическую шестерню, составляющую одно целое с валом и перемещающуюся по зубчатой рейке, которая шарнирно связана с рулевыми тягами. При изменении положения руля на определенный угол рейка совершает движение в горизонтальной плоскости и через тяги поворачивает колеса. Пара шестерня-рейка находится в корпусе редуктора, который расположен в подрамнике подвески.
Некоторые автомобили снабжены рулевым механизмом с переменным передаточным отношением, где применена зубчатая рейка с различным профилем зубьев: в околонулевой зоне зубья имеют форму треугольника, а ближе к краям – вид трапеции. Конструкция рейки с различной геометрией зубьев способствует изменению передаточного числа в паре шестерня-рейка, уменьшая угол поворота рулевого колеса. Благодаря этой схеме управлять автомобилем намного удобнее, динамичнее, и требуется меньше усилий, прилагаемых к рулевому колесу.
Отдельные производители авто используют на автомобилях рулевые механизмы с управлением на четыре колеса. Конструкция позволяет добиться более эффективного управления и обеспечивает стабильность машины при движении на высокой скорости. Благодаря такому техническому решению передние и задние колеса авто получили синхронизацию при повороте в ту или иную сторону. Кроме того, улучшилась маневренность в случае, когда автомобиль движется с малой скоростью: передние и задние колеса могут быть повернуты в разном направлении. Это достигается за счет того, что при большой скорости автомобиля сайлентблоки, установленные на задней подвеске, под воздействием сил во время поворота авто деформируются, не давая колесам существенно изменить угол поворота.
Рулевой привод представляет собой шарнирно-рычажную конструкцию, посредством которой усилия, прилагаемые к рулю, передаются напрямую колесам, обеспечивая при этом устойчивость автомобиля при повороте. Кроме этого, конструкция удерживает колеса при работе подвески, тип которой зависит от устройства рулевого привода.
Наиболее популярна механическая конструкция рулевого привода, включающая в себя рулевые тяги и шаровые опоры (рулевые шарниры). В свою очередь, шаровой шарнир, защищенный от износа вкладышами, находится в корпусе с закрытым резиновым пыльником, который препятствует проникновению пыли и грязи в шарнирное соединение. Шаровой шарнир изготовлен как одно целое с шаровым пальцем, который служит наконечником для рулевых тяг и составляет с ними дополнительный рычаг подвески.
Для регулировки рулевого управления существует несколько параметров, влияющих на устойчивость автомобиля во время движения, и на усилие, прилагаемое к рулю. Четыре наиболее важных из них касаются угловых регулировок: развал, схождение, угол продольного и поперечного наклона поворотной ступицы колеса, а также две регулировки плеча (стабилизация и обкатка). Стоит заметить, что все регулировки связаны между собой и оказывают важное влияние на работу всего рулевого управления.
Современные автомобили уже не обходятся без усилителя рулевого управления, которое значительно уменьшает усилие, приложенное к рулю, позволяет точно и быстро реагировать на окружающую обстановку при движении. Благодаря усилителю руля водитель меньше утомляется, да и передаточное число шестерен в редукторе можно уменьшить, что делает его более компактным. По своему типу привод усилителя делится на электрический, гидравлический или пневматический. Последний больше относится к автомобилям грузового класса.
В большинстве своем автомобили нынешнего поколения снабжены гидравлическим усилителем рулевого управления, называемым для простоты «гидроусилитель руля». Кроме этого, существует его вариант – электрогидравлический усилитель, в котором жидкость нагнетается насосом с приводом от электродвигателя. Однако прогрессивным считается применяемый сегодня электрический усилитель руля, в котором крутящий момент вала электродвигателя подается непосредственно на карданный вал рулевого колеса или прямо на рулевой редуктор. А использование электроники делает возможным применение электроусилителя при парковке в автоматическом режиме или в системе, которая помогает удерживать автомобиль на полосе движения.
Инновационным усилителем руля можно считать адаптивный усилитель рулевого управления, благодаря которому усилие, прилагаемое при повороте колеса, зависит от скорости движения. Как пример подобной конструкции можно привести известный адаптивный гидравлический усилитель Servotronic. К новинке можно отнести и систему активного рулевого управления BMW, а также систему динамического рулевого управления от Audi, в котором передаточное число редуктора рулевого механизма зависит от скорости движения автомобиля.
Тема 8. Система управления автомобилем8.1. Рулевое управление
Рулевое управление служит для изменения направления движения автомобиля поворотом передних управляемых колес. Оно состоит из рулевого механизма и рулевого привода.
8.1.1. Назначение рулевого управления и схема поворота автомобиля
Рулевой механизм преобразует вращение рулевого колеса в поступательное перемещение тяг привода, вызывающее поворот управляемых колес. При этом усилие, передаваемое водителем, от рулевого колеса к поворачиваемым колесам, возрастает во много раз.
Рулевой привод совместно с рулевым механизмом передает управляющее усилие от водителя непосредственно к колесам и обеспечивает этим поворот управляемых колес на задаваемый угол.
Рис. 8.1. Схема поворота автомобиля
Чтобы совершить поворот без бокового скольжения колес, все они должны катиться по дугам разной длины, описанным из центра поворота О см. рис. При этом передние управляемые колеса должны поворачиваться на разные углы. Внутреннее по отношению к центру поворота колесо должно поворачиваться на угол альфа-В, наружное - на меньший угол альфа-Н. Это обеспечивается соединением тяг и рычагов рулевого привода в форме трапеции. Основанием трапеции служит балка 1 переднего моста автомобиля, боковыми сторонами являются левый 4 и правый 2 поворотные рычаги, а вершину трапеции образует поперечная тяга 3, которая соединяется с рычагами шарнирно. К рычагам 4 и 2 жестко присоединены поворотные цапфы 5 колес. Один из поворотных рычагов, чаще всего левый рычаг 4, имеет связь с рулевым механизмом через продольную тягу 6. Таким образом, при приведении в действие рулевого механизма продольная тяга, перемещаясь вперед или назад, вызывает поворот обоих колес на разные углы в соответствии со схемой поворота.
Расположение и взаимодействие деталей рулевого управления, не имеющего усилителя, можно рассмотреть на схеме (рис.8.3).
Сначала рассмотрим устройство червячной передачи (рис. 8.2)
Передача предназначена для существенного увеличения крутящего момента и, соответственно, уменьшения угловой скорости. Ведущим звеном является червяк. Червячная передача без смазки и вибрации обладает эффектом самоторможения и является необратимой: если приложить момент к ведомому звену (червячному колесу), из-за сил трения передача работать не будет. Передаточные отношения червячной передачи закладываются в пределах от 8 до 100, а в некоторых приложениях - до 1000.
Рис. 8.2. Червячная передача
Рассмотрим расположение и взаимодействие деталей рулевого управления, не имеющего усилителя:
Рулевой механизм состоит из рулевого колеса 3, рулевого вала 2 и рулевой передачи 1, образованной зацеплением червяка с червячным роликом, на вал которого крепится сошка 9 рулевого привода. Сошка и все остальные детали рулевого управления: продольная тяга 8, верхний рычаг левой поворотной цапфы 7, нижние рычаги 5 левой и правой поворотных цапф, поперечная тяга 6 составляют рулевой привод.
Рис. 8.3. Схемы рулевого управления
Поворот управляемых колес происходит при вращении рулевого колеса 3, которое через вал 2 передает вращение рулевой передаче 1. При этом червяк передачи, находящийся в зацеплении с сектором, начинает перемещать сектор вверх или вниз по своей нарезке. Вал сектора приходит во вращение и отклоняет сошку 9, которая своим верхним концом насажена на выступающую часть вала сектора. Отклонение сошки передается продольной тяге 8, которая перемещается вдоль своей оси. Продольная тяга 8 связана через верхний рычаг 7 с поворотной цапфой 4, поэтому ее перемещение вызывает поворот левой поворотной цапфы. От нее усилие поворота через нижние рычаги 5 и поперечную тягу 6 передается правой цапфе. Таким образом происходит поворот обоих колес.
Управляемые колеса поворачиваются рулевым управлением на ограниченный угол, равный 28-35°. Ограничение вводится для того, чтобы исключить при повороте задевание колесами деталей подвески или кузова автомобиля.
Конструкция рулевого управления очень сильно зависит от типа подвески управляемых колес. При зависимой подвеске передних колес в принципе сохраняется схема рулевого управления, приведенная на (рис. 8.3 а), при независимой подвеске (рис. 8.3 б) рулевой привод несколько усложняется.
8.1.2. Рулевой механизм
Он обеспечивает поворот управляемых колес с небольшим усилием на рулевом колесе. Это может быть достигнуто за счет увеличения передаточного числа рулевого механизма. Однако передаточное число ограничено количеством оборотов рулевого колеса. Если выбрать передаточное число с количеством оборотов рулевого колеса больше 2-3, то существенно увеличивается время, требуемое на поворот автомобиля, а это недопустимо по условиям движения. Поэтому передаточное число в рулевых механизмах ограничивают в пределах 20-30, а для уменьшения усилия на рулевом колесе в рулевой механизм или привод встраивают усилитель.
Ограничение передаточного числа рулевого механизма также связано со свойством обратимости, т. е. способностью передавать обратное вращение через механизм на рулевое колесо. При больших передаточных числах увеличивается трение в зацеплениях механизма, свойство обратимости пропадает, и самовозврат управляемых колес после поворота в прямолинейное положение оказывается невозможным.
Рулевые механизмы в зависимости от типа рулевой передачи разделяют на:
червячные
винтовые
реечные
комбинированные
В винтовом механизме вращение винта, связанного с рулевым валом, передается гайке, которая заканчивается рейкой, зацепленной с зубчатым сектором, а сектор установлен на одном валу с сошкой. Такой рулевой механизм образован рулевой передачей типа винт-гайка-сектор.
В шестеренчатых рулевых механизмах рулевая передача образуется цилиндрическими или коническими шестернями, к ним же относят передачу типа шестерня-рейка. В последних, цилиндрическая шестерня связана с рулевым валом, а рейка, зацепленная с зубьями шестерни, выполняет роль поперечной тяги. Реечные передачи и передачи типа червяк-ролик преимущественно применяют на легковых автомобилях, так как обеспечивают сравнительно небольшое передаточное число. Для грузовых автомобилей используют рулевые передачи типа червяк-сектор и винт-гайка-сектор, снабженные либо встроенными в механизм усилителями, либо усилителями, вынесенными в рулевой привод.
8.1.3. Рулевой привод
Конструкции рулевого привода различаются расположением рычагов и тяг, составляющих рулевую трапецию, по отношению к передней оси. Если рулевая трапеция находится впереди передней оси, то такая конструкция рулевого привода называется передней рулевой трапецией, при заднем расположении - задней трапецией. Большое влияние на конструктивное исполнение и схему рулевой трапеции оказывает конструкция подвески передних колес.
При зависимой подвеске рулевой привод имеет более простую конструкцию, так как состоит из минимума деталей. Поперечная рулевая тяга в этом случае сделана цельной, а сошка качается в плоскости, параллельной продольной оси автомобиля. Можно сделать привод и с сошкой, качающейся в плоскости, параллельной переднему мосту. Тогда продольная тяга будет отсутствовать, а усилие от сошки передается прямо на две поперечные тяги, связанные с цапфами колес.
При независимой подвеске передних колес схема рулевого привода конструктивно сложнее. В этом случае появляются дополнительные детали привода, которых нет в схеме с зависимой подвеской колес. Изменяется конструкция поперечной рулевой тяги (рис. 8.3.) Она выполнена расчлененной, состоящей из трех частей: основной поперечной тяги 4 и двух боковых тяг - левой 3 и правой 6. Для опоры основной тяги 4 служит маятниковый рычаг 5, который по форме и размерам соответствует сошке 1. Соединение боковых поперечных тяг с поворотными рычагами 2 цапф и с основной поперечной тягой выполнено с помощью шарниров, которые допускают независимые перемещения колес в вертикальной плоскости. Рассмотренная схема рулевого привода применяется главным образом на легковых автомобилях.
Рулевой привод, являясь частью рулевого управления автомобиля, обеспечивает не только возможность поворота управляемых колес, но и допускает колебания колес при наезде ими на неровности дороги. При этом, детали привода получают относительные перемещения в вертикальной и горизонтальной плоскостях и на повороте передают усилия, поворачивающие колеса. Соединение деталей при любой схеме привода производят с помощью шарниров шаровых либо цилиндрических.
8.1.4. Рулевой механизм с передачей типа червяк - ролик
Широко распространен на легковых и грузовых автомобилях. См. рис 8.4.
Основными деталями рулевого механизма являются рулевое колесо 4, рулевой вал 5, установленный в рулевой колонке 3 и соединенный с глобоидным червяком 1. Червяк установлен в картере 6 рулевой передачи на двух конических подшипниках 2 и зацеплен с трехгребневым роликом 7, который вращается на шарикоподшипниках на оси. Ось ролика закреплена в вильчатом кривошипе вала 8 сошки, опирающемся на втулку и роликовый подшипник в картере 6. Зацепление червяка и ролика регулируют болтом 9, в паз которого вставлен ступенчатый хвостовик вала сошки. Фиксация заданного зазора в зацеплении червяка с роликом производится фигурной шайбой со штифтом и гайкой.
Картер 6 рулевой передачи закреплен болтами к лонжерону рамы. Верхний конец рулевого вала имеет конические шлицы, на которые посажено и закреплено гайкой рулевое колесо.
. Рис. 8.4. Рулевой механизм автомобиля ГАЗ-53А
8.1.5. Рулевой механизм с передачей типа винт - гайка - рейка - сектор с усилителем
Рассмотрим устройство механизма на примере автомобиля ЗИЛ-5301. На этом автомобиле рулевой механизм объединен с усилителем
Рис. 8.5. Рулевой механизм с гидроусилителем
Рулевой механизм с гидроусилителем состоит из корпуса (цилиндра) усилителя 2, герметично закрытого нижней крышкой 1 и промежуточной крышкой 8. Внутри цилиндра находится поршень-рейка 3.Поршень в цилиндре уплотнен кольцами. В выточку поршня вставлена шариковая гайка 5, закрепленная в поршне установочными винтами 21. Через гайку и поршень проходит рулевой винт 4. На винте и внутри шариковой гайки нарезаны спиральные канавки, в которые вложены шарики 7. Они являются шариковой резьбой, облегчающей вращение рулевого винта. Для обеспечения циркуляции шариков начало и конец шариковой резьбы соединены желобом 6. Поршень имеет зубчатую рейку для зацепления с зубчатым сектором 22, выполненным заодно с валом рулевой сошки 18. Зацепление сектора с рейкой регулируется винтом 16.
От самопроизвольного вращения винт удерживается контргайкой. Вал сошки установлен в корпусе на двух втулках, одна из которых установлена в боковой крышке, а другая в приливе корпуса. Этот конец вала уплотнен сальником, на его конических шлицах установлена сошка, которая закреплена стопорной шайбой и гайкой.
Внизу картера рулевого механизма имеется отверстие для слива рабочей жидкости, закрывающееся пробкой 17.
В верхней части цилиндра закреплен корпус клапана управления 10. Внутри его на рулевом винте 4 между двумя шариковыми подшипниками находится золотник 9 клапана. В среднем, нейтральном положении золотник удерживается двенадцатью реактивными плунжерами 20 и пружинами 19. Подшипники и золотник зажимаются регулировочной гайкой 11 и от среднего положения могут перемещаться вместе с рулевым винтом на 1…1,5 мм.
Принцип действия гидроусилителя следующий: насос нагнетает давление в системе, но если руль стоит на месте, то насос просто создает циркуляцию жидкости. Стоит только водителю начать поворачивать руль, как перекрывается циркуляция, и жидкость начинает давить на рейку, «помогая» водителю. Давление направлено в ту сторону, в которую вращается руль
8.1.6. Реечный рулевой механизм Рис. 8.6. Реечный рулевой механизм
Самая распространенная система в настоящее время. Основные узлы это: рулевое колесо (руль), рулевой вал (то же что и в червячном механизме), рулевая рейка – это узел, состоящий из зубчатой рейки, в движение которую приводит рулевая шестерня. Собранная в одном корпусе, чаще из легкого сплава, крепится непосредственно к кузову авто. На концах зубчатой рейки изготовлены резьбовые отверстия для крепления рулевых тяг. Рейка «выезжает» из корпуса влево или вправо. Усилие передается на рулевой рычаг с наконечником. Наконечник вставлен в ступицу, которую и поворачивает в дальнейшем. Для уменьшения усилия водителя при вращении рулевого колеса, в реечное рулевое устройство были введены усилители руля. Усилитель руля является вспомогательным устройством для вращения рулевого колеса.
Различают несколько типов усилителей руля:
гидроусилитель
гидроэлектроусилитель
электроусилитель
пневмоусилитель
В гидроэлектроусилителе система точно такая же, только насос вращает электромотор.
В электроусилителе применяется так же электромотор, но соединяется он непосредственно с рейкой или с рулевым валом. Управляется электронным блоком управления. Электроусилитель еще называют адаптивным усилителем из-за возможности прикладывания разного усилия к вращению рулевого колеса, в зависимости от скорости движения. Известная система Servotronic.
Пневмоусилитель это близкая «родня» гидроусилителя, только жидкость заменена на сжатый воздух.
8.1.7. Активная рулевая система
Рис. 8.7.
Самая современная система управления в настоящее время. В состав входит: рулевая рейка с планетарным механизмом и электродвигателем, блок электронного управления, рулевые тяги, наконечники, рулевое колесо.
Принцип работы рулевой системы чем-то напоминает работу АКПП. При вращении рулевого колеса, вращается планетарный механизм, который и приводит в действие рейку, но передаточное число всегда разное, в зависимости от скорости движения автомобиля. Так как солнечную шестерню снаружи вращает электродвигатель, то в зависимости от скорости вращения изменяется передаточное число. На небольшой скорости коэффициент передачи составляет единицу. Но при большем разгоне, когда малейшее движение руля может привести к негативным последствиям, включается электромотор, вращает солнечную шестерню, соответственно необходимо руль довернуть больше при повороте. На маленькой скорости автомобиля электродвигатель вращается в обратную сторону, создавая более комфортное управление.
8.1.8. Рулевая колонка
У различных автомобилей устройство рулевой колонки несколько отличается. В качестве примера рассмотрим устройство рулевой колонки автомобиля ГАЗ 31029 (Волга).
Основной ее частью является рулевое колесо 12 (рис. 8.8)
Рис. 8.8.
Оно устанавливается на мелких конических шлицах верхнего вала 7 и крепится на нем га йкой 8. Верхний вал вращается в шариковом подшипнике 22 и с помощью эластичной муфты соединяется с нижним валом. Муфта обеспечивает передачу вращения с вала на вал под некоторым углом. Рулевая колонка крепится с помощью хомута 18. Мягкое крепление рулевой колонки обеспечивается резиновыми шайбами 15. Под кожухом рулевой колонки 6 установлены корпус выключателя зажигания и противоугонного устройства 20, выключатель зажигания, стартера и противоугонного устройства 21, основание переключателя света фар и указателей поворота 3.
Для включения противоугонного устройства ключ зажигания нужно повернуть против хода часовой стрелки до конца и вынуть его из выключателя. При этом защелка противоугонного устройства войдет в один из пазов верхнего вала 7 и зафиксирует его. При отпирании противоугонного устройства для облегчения поворота ключа необходимо слегка покачивать рулевое колесо из стороны в сторону.
Рулевая колонка крепится к панели приборов хомутом 18 и двумя болтами 17. Между хомутом и панелью установлены 2 втулки 16 и резиновые шайбы 15. Такое крепление рулевой колонки дает ей возможность перемещаться вниз в случае столкновения автомобиля с препятствием.
Верхний и нижний рулевые валы соединяются эластичной энергопоглащающей, безопасное муфтой, предназначенной для смягчения удара водителя о рулевое колесо при аварийных столкновениях.
Рис. 8.9.
Состоит муфта из 2 фланцев 1 со скосами и 2 предохранительных пластин 2. Между ними установлена резиновая шайба 6. Детали муфты соединяются 4 шпильками 4 и гайками. Имеются усилительные 5 и стопорные 7 пластины.
8.1.9. Особенности рулевого привода легковых и грузовых автомобилей
Рулевой привод легковых заднеприводных автомобилей состоит из боковых рычагов поворотных кулаков 1 и регулировочных трубок 3 с наконечником тяги 2.
Рис. 8.10
Регулирование схождения колес производится изменением длины боковых тяг за счет регулировочных трубок. Трубки имеют с одной стороны правую резьбу, а с другой – левую. От самопризвольного вращения трубки удерживаются стяжными хомутами 4 и болтами 5. Поперечная тяга 7 соединяется с сошкой 6 и маятниковым рычагом 8.
Шарниры рулевых тяг. Все шарниры – самоподтягивающиеся с полусферическими пальцами.
Рис. 8.11
Шарнир наконечника и средней тяги рулевой трапеции состоит из шарового пальца, находящегося в корпусе 5. Верхней сферической частью палец опирается на внутреннюю сферу корпуса. Пальцы запрессовываются в проушины тяг и наконечников и крепятся в них корончатыми гайками. После затяжки гайки шплинтуются. Корпус шарнира запрессовывается в проушину тяги 3.
От попадания пыли и грязи шарнир защищен гофрированным резиновым чехлом 2. Шаровой палец, кроме верхней, имеет еще и нижнюю сферу, на которую опирается опорная пята 4, поджимаемая пружиной. Давление пружины устраняет люфт в шарнире. Крепится палец в корпусе шарнира заглушкой 6 и шплинтом 7.
Шарнир тяги сошки (рис. 8.11 б) отличается устройством уплотнителя 8 тяги сошки и маятникового рычага. Он не гофрированный и имеет распорную втулку 9.
Маятниковый рычаг. Поперечная тяга с одной стороны подвешена на сошке руля, а с другой – на маятниковом рычаге. Маятниковый рычаг в корпусе – кронштейне вращается в двух металлокерамических втулках, которые запрессованы в резиновые защитные втулки.
Одна втулка прижата своим торцом к плоскости бобышки маятникового рычага, а другая к шайбе. Шайба вращается вместе с пальцем. Втулки входят в кронштейн с зазором, что позволяет переднему концу маятникового рычага упруго перемещаться до 2-4 мм за счет деформации резиновых втулок. Это перемещение не влияет на устойчивость и безопасность движения автомобиля, а также на износ шин.
На переднем конце маятникового рычага установлен шаровой шарнир, одинаковый с шарниром сошки. Отличается он тем, что в нем установлен полиэтиленовый сухарь, который удерживает палец внутри корпуса в определенном положении.
Рулевой привод легковых переднеприводных автомобилей
Рис. 8.12
Рычаги 3 и 7 на концах имеют левую и правую резьбу, соединяются между собой регулировочной муфтой 6, которая также имеет резьбу на концах (левую и правую). Соединение муфты с рычагами фиксируется гайками 4. Вращением регулировочной муфты конструкция может удлиняться или укорачиваться, что приводит к изменению угла схождения колес.
Рулевой привод грузовых автомобилей. В отличие от легковых автомобилей, грузовые имеют продольную тягу 3 (рис. 8.13).
Рис. 8.13
Усилие с вала сошки у грузовых автомобилей передается на сошку, на продольную рулевую тягу, рычаг продольной рулевой тяги, поворотный кулак, левый рычаг поперечной рулевой тяги, правый рычаг поперечной рулевой тяги и на правый поворотный кулак.
Рулевые рычаги соединяются с тягами шарнирно. Шаровые сочленения имеют различную конструкцию и тщательно защищены от попадания грязи; смазка подается в них через масленки. В некоторых моделей автомобилей в сочленениях тяг применяются пластмассовые вкладыши, не требующие смазки.
Шарнирное соединение продольной рулевой тяги (рис. 8.14 а) имеет вкладыши 1 и 3, охватывающие шаровой палец 2. Пружина 4 смягчает удары от колес и устраняет зазоры при износе сочленения. Для ограничения сжатия пружины (во избежание ее поломки) устанавливаются упоры 5. Зазор в сочленениях устраняют резьбовой пробкой 6.
В поперечных тягах (рис. 8.14 б,в) применяются эксцентриковые вкладыши (наконечники) 9, прижимаемые к шаровому пальцу пружиной, установленной снизу. При таком устройстве пружины не нагружаются силами, действующими на поперечную рулевую тягу, а устранение зазора при износе сочленений происходит автоматически. Концы поперечной тяги и наконечники 7 имеют правую и левую резьбу для регулировки длины тяги (регулировка сходимости колес).
После регулировки наконечники затягиваются болтами 8.
Рис. 8.14
8.2. Тормозная система
8.2.1. Назначение и виды тормозных систем
Тормозная система предназначена для управляемого изменения скорости автомобиля, его остановки, а также удержания на месте длительное время за счет использования тормозной силы между колесом и дорогой. Тормозная сила может создаваться колесным тормозным механизмом, двигателем автомобиля (т.н. торможение двигателем), гидравлическим или электрическим тормозом-замедлителем в трансмиссии.
Для реализации указанных функций на автомобиле устанавливаются следующие виды тормозных систем :
рабочая;
запасная;
стояночная.
Тормозной механизм предназначен для создания тормозного момента, необходимого для замедления и остановки автомобиля.
На автомобилях устанавливаются фрикционные тормозные механизмы, работа которых основана на использовании сил трения. Тормозные механизмы рабочей системы устанавливаются непосредственно в колесе. В зависимости от конструкции фрикционной части различают:
барабанные тормозные механизмы;
дисковые тормозные механизмы.
В качестве вращающейся части барабанного механизма используется тормозной барабан, неподвижной части – тормозные колодки
Вращающаяся часть дискового механизма представлена тормозным диском, неподвижная – тормозными колодками. Тормозные колодки прижимаются к суппорту пружинными элементами. К колодкам прикреплены фрикционные накладки.
8.2.2.1. Устройство дискового механизма легковых и малотоннажных грузовых автомобилей
Дисковый тормозной механизм (рис.8.14) состоит из:
Рис. 8.15 Схема работы дискового тормозного механизма 1 - наружный рабочий цилиндр (левого) тормоза; 2 - поршень; 3 - соединительная трубка; 4 - тормозной диск переднего (левого) колеса; 5 - тормозные колодки с фрикционными накладками; 6 - поршень; 7 - внутренний рабочий цилиндр переднего (левого) тормоза
Суппорт закреплен на поворотном кулаке переднего колеса автомобиля. В нем находятся два тормозных цилиндра и две тормозные колодки. Колодки с обеих сторон «обнимают» тормозной диск, который вращается вместе с закрепленным на нем колесом. При нажатии на педаль тормоза поршни начинают выходить из цилиндров и прижимают тормозные колодки к диску. После того, как водитель отпустит педаль, колодки и поршни возвращаются в исходное положение за счет легкого «биения» диска. Дисковые тормоза очень эффективны и просты в обслуживании.
Преимущества дисковых тормозов :
при повышении температуры характеристики дисковых тормозов довольно стабильны, тогда как у барабанных снижается эффективность
температурная стойкость дисков выше, в частности, из-за того, что они лучше охлаждаются
более высокая эффективность торможения позволяет уменьшить тормозной путь
меньшие вес и размеры
повышается чувствительность тормозов
время срабатывания уменьшается
изношенные колодки просто заменить, на барабанных приходится предпринимать усилия на подгонку колодок чтобы одеть барабаны
около 70% кинетической энергии автомобиля гасится передними тормозами, задние дисковые тормоза позволяют снизить нагрузку на передние диски
температурные расширения не влияют на качество прилегания тормозных поверхностей
Барабанный тормозной механизм (рис. 8.15) состоит из:
тормозного щита
тормозного цилиндра
двух тормозных колодок
стяжных пружин
тормозного барабана
Рис. 8.16 Схема работы барабанного тормозного механизма 1 - тормозной барабан; 2 - тормозной щит; 3 - рабочий тормозной цилиндр; 4 - поршни рабочего тормозного цилиндра; 5 - стяжная пружина; 6 - фрикционные накладки; 7 - тормозные колодки
Тормозной щит жестко крепится на балке заднего моста автомобиля, а на щите, в свою очередь, закреплен рабочий тормозной цилиндр. При нажатии на педаль тормоза поршни в цилиндре расходятся и начинают давить на верхние концы тормозных колодок. Колодки в форме полуколец прижимаются своими накладками к внутренней поверхности круглого тормозного барабана, который при движении автомобиля вращается вместе с закрепленным на нем колесом. Торможение колеса происходит за счет сил трения, возникающих между накладками колодок и барабаном. Когда же воздействие на педаль тормоза прекращается, стяжные пружины оттягивают колодки на исходные позиции.
Преимущества барабанных тормозов:
низкая стоимость, простота производства
обладают эффектом механического самоусиления
8.2.3. Назначение и виды тормозного привода легковых и малотоннажных грузовых автомобилей
Тормозной привод обеспечивает управление тормозными механизмами. В тормозных системах автомобилей применяются следующиетипы тормозных приводов:
механический;
гидравлический;
Гидравлический привод является основным типом привода в рабочей тормозной системе. Достоинства гидропривода:
малое время срабатывания;
равенство приводных сил на тормозных механизмах левых и правых колес;
удобство компоновки (в отличие от механического привода гидролиния может быть проложена в любом, удобном для монтажа месте);
высокий КПД (до 0,95);
возможность распределения приводных усилий между тормозными механизмами передних и задних колес в результате применения рабочих цилиндров разного диаметра;
простота обслуживания;
К недостаткам тормозного гидропривода относят:
· снижение КПД при низких температурах;
· угроза разгерметизации и попадания воздуха, чего трудно избежать (например, при составлении автопоезда);
· образование паровых пробок и «проваливание» педали с потерей эффективности торможения при закипании тормозной жидкости из-за нагрева тормозных механизмов при длительном торможении.
Конструкция гидравлического привода включает:
тормозную педаль;
усилитель тормозов;
главный тормозной цилиндр;
колесные цилиндры;
регулятор давления тормозов
сигнальное устройство
трубопроводы и шланги
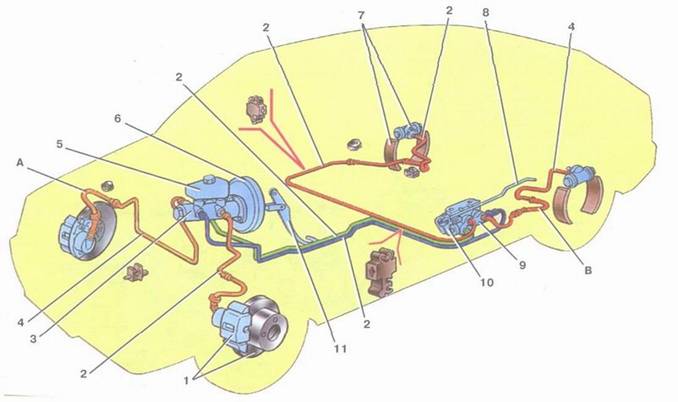
Тормозная педаль передает усилие от ноги водителя на главный тормозной цилиндр.
Вакуумный усилитель применяется для уменьшения усилия при нажатии на педаль тормоза. Усилитель заметно облегчает работу водителя, т.к. использование педали тормоза при движении в городском цикле носит постоянный характер и довольно быстро утомляет. Вакуумный усилитель (рис. 8.16) конструктивно связан с главным тормозным цилиндром. Основным элементом усилителя является камера, разделенная резиновой перегородкой (диафрагмой) на два объема. Один объем связан с впускным трубопроводом двигателя, где создается разрежение около 0,8 кг/см², а другой сообщается с атмосферой (1 кг/см²). Из-за перепада давления в 0,2 кг/см², благодаря большой площади диафрагмы, "помогающее" усилие на педали тормоза может достигать 30–40 кг и более.
Рис. 8.18 Схема вакуумного усилителя 1 – главный тормозной цилиндр; 2 – корпус вакуумного усилителя; 3 – диафрагма; 4 – пружина; 5 – педаль тормоза
Рис. 8.19 Вакуумный усилитель
Главный тормозной цилиндр создает давление тормозной жидкости и нагнетает ее к тормозным цилиндрам. На современных автомобилях применяется сдвоенный главный тормозной цилиндр, который создает давление для двух контуров.
Главный тормозной цилиндр – центральный конструктивный элемент рабочей тормозной системы. Он преобразует усилие, прикладываемое к педали тормоза, в гидравлическое давление в тормозной системе. Работа главного тормозного цилиндра основана на свойстве тормозной жидкости, не сжиматься под действием внешних сил.
Рис. 8.20. Главный тормозной цилиндр АЗЛК 2141 1 – стопорное кольцо; | 41 – двойной клапан; |
Главный тормозной цилиндр закреплен на крышке вакуумного усилителя. Над цилиндром расположен двухсекционный бачок с запасом тормозной жидкости, который соединяется с секциями главного цилиндра через компенсационные и перепускные отверстия. Бачок служит для пополнения жидкости в тормозной системе в случае небольших ее потерь (утечки, испарение). Стенки бачка прозрачные, на них выполнены контрольные метки, что позволяет визуально отслеживать уровень тормозной жидкости. В бачке также устанавливается датчик уровня тормозной жидкости. При падении уровня тормозной жидкости ниже установленного на панели приборов загорается сигнальная лампа.
В корпусе главного тормозного цилиндра расположены друг за другом два поршня. В первый поршень упирается шток вакуумного усилителя тормозов, второй поршень установлен свободно. Уплотнение поршней в корпусе цилиндра выполнено с помощью резиновых манжет. Возвращение и удержание поршней в исходном положении обеспечивают две возвратные пружины.
При торможении шток вакуумного усилителя тормозов толкает первый поршень. При движении по цилиндру поршень перекрывает компенсационное отверстие. Давление в первом контуре начинает расти. Под действием этого давления перемещается второй контур, давление во втором контуре также начинает расти. В образовавшиеся при движении поршней пустоты заполняются через перепускное отверстие тормозной жидкостью. Перемещение каждого из поршней происходит до тех пор, пока позволяет возвратная пружина. При этом в контурах создается максимальное давление, обеспечивающее срабатывание тормозных механизмов.
При окончании торможения поршни под действием возвратных пружин возвращаются в исходное положение. Когда поршень проходит через компенсационное отверстие, давление в контуре выравнивается с атмосферным давлением. Даже если тормозная педаль отпускается резко, разряжения в рабочих контурах не создается. Этому препятствует тормозная жидкость, заполнившая полости за поршнями. При движении поршня эта жидкость плавно возвращается (перепускается) в бачок через перепускное отверстие.
Привод рабочей тормозной системы с целью повышения надежности действия должен иметь не менее двух независимых контуров. В случае повреждения одного из контуров второй контур обеспечивает торможение автомобиля. Наибольшее распространение получили двухконтурные тормозные приводы, возможные принципиальные схемы которых приведены на рис. 8.19. Для разделения контуров применяются двухсекционные органы управления (главный цилиндр, регулятор давления). Каждая секция такого органа обслуживает один контур тормозного привода.
А) б) в) Рис. 8.21 Схемы двухконтурных тормозных приводов
Наиболее часто используется принцип деления привода по осям автомобиля (рис. б). Такая схема является самой простой, но при этом значительно снижается эффективность торможения при выходе из строя контура передних тормозов. При диагональной схеме (рис. в) сохраняется хорошая эффективность торможения, но резко снижается устойчивость автомобиля при выходе из строя одного из контуров, особенно при торможении на повороте.
Отмеченные недостатки обеих схем устраняются полностью или частично в двухконтурных приводах с использованием принципа дублирования (рис.а).
Если в одном из контуров произойдет утечка тормозной жидкости, другой контур будет продолжать работать. Например, при утечке в первом контуре первый поршень беспрепятственно переместиться по цилиндру до соприкосновения со вторым поршнем. Второй поршень начинает перемещаться, обеспечивая срабатывание тормозных механизмов во втором контуре.
При утечке во втором контуре, работа главного тормозного цилиндра происходит несколько иначе. Движение первого поршня вовлекает в движение второй поршень, который не встречает препятствий на своем пути. Он двигается до достижения упором торца корпуса цилиндра. После чего давление в первом контуре начинает расти, обеспечивая торможение автомобиля.
Несмотря на то, что ход педали тормоза при утечке жидкости несколько увеличивается, торможение будет достаточно эффективным.
Над главным цилиндром находится расширительный бачок, предназначенный для пополнения тормозной жидкости в случае небольших потерь.
Рис. 8.22 Главный тормозной цилиндр с расширительным бачком
Колесный цилиндр обеспечивает срабатывание тормозного механизма, т.е. прижатие тормозных колодок к тормозному диску или барабану.
Рис. 8.23 Колесный цилиндр барабанного тормозного механизма (задних колес) 1. Поршень колесного цилиндра; 2. Кольцо резиновое; 3. Манжета поршня; 4. Пружина поршня;
5. Защитный колпак колесного цилиндра.
Рис. 8.24. Тормозной барабанный механизм заднего колеса 1 - колесный цилиндр; 2 - верхняя стяжная пружина колодок; 3 - накладка колодки; 4 - щит тормоза; 5 - внутренняя пластина; 6 - оболочка заднего троса; 7 - нижняя стяжная пружина колодок; 8 - передняя тормозная колодка; 9 - опорная пластина колодок; 10 - заклепки; 11 - маслоотражатель; 12 - направляющая пластина колодок; 13 - задний трос стояночного тормоза; 14 - пружина заднего троса; 15 - наконечник заднего троса; 6 - задняя тормозная колодка; 17 - опорная стойка колодки; 18 - рычаг ручного привода колодок; 19 - резиновые подушки; 20 - распорная планка колодок; 21 - палец рычага ручного привода колодок
Рис. 8.15. Тормозной дисковый механизм переднего колеса
Рис. 8.25 Колесный цилиндр дискового тормозного механизма (передних колес)
Регулятор давления тормозов. Регулятор давления тормозов регулирует давление в гидравлическом приводе тормозных механизмов задних колес в зависимости от нагрузки на заднюю ось автомобиля. Регулятор давления тормозов включен в оба контура тормозной системы, и через регулятор давления тормозов тормозная жидкость поступает к обоим задним тормозным механизмам.
Регулятор давления тормозов 1 (рис. 8.24) прикреплен к кронштейну 9 двумя болтами 2 и 16. При этом передний болт 2 одновременно крепит вильчатый кронштейн 3 рычага 5 привода регулятора давления тормозов. На пальце этого кронштейна шарнирно штифтом 4 закреплен двуплечий рычаг 5. Его верхнее плечо связано с упругим рычагом 10, другой конец которого через серьгу 11 шарнирно соединен с кронштейном рычага задней подвески.
Кронштейн 3 вместе с рычагом 5 за счет овальных отверстий под болт крепления можно перемещать относительно регулятора давления. Таким образом, регулируется усилие, с которым рычаг 5 действует на поршень регулятора давления тормозов.
В случае не нагруженной задней оси автомобиля, поршень регулятора давления, действуя на клапан, уменьшает диаметр сечения трубопровода. И, наоборот, если автомобиль перегружен, то регулятор давления увеличивает диаметр сечения, усиливая действие тормозного механизма.
Рис. 8.26 Регулятор давления тормозов
Сигнальное устройство оповещает водителя о потере давления в одном из контуров гидравлического привода, вызванной выходом из строя шланга или трубопровода. В этом случае на приборном щетке загорается контрольная лампочка. Эффективность торможения снижается примерно в 2 раза, поэтому эксплуатация автомобиля становится недопустимой.
Трубопроводы и шланги
8.2.4. Антиблокировочный механизм тормозной системы
Заторможенные нескользящие колеса воспринимают большую тормозную силу, чем при движении юзом, т.к. коэффициент сцепления при частичном проскальзывании колес больше, чем при полном скольжении. При полном скольжении в контакте с дорогой находятся одни и те же части шин. Они нагреваются и за счет шероховатости дороги сильно изнашивается. Продукты трения при этом создают скользкую поверхность, за счет которой уменьшается коэффициент сцепления колес с дорогой и начинается боковой увод колес, особенно передних.
Антиблокировочные системы (АБС) предназначены для удерживания колес на грани движения юзом, не допуская начала скольжения, чтобы колеса воспринимали большую тормозную силу. АБС автоматически уменьшают тормозной момент при начале скольжения колес и через некоторое время (0,05…0,1 сек) вновь увеличивают его. Колеса автомобиля, благодаря такому циклическому нагружению тормозным моментом, катятся с частичным проскальзыванием, и коэффициент сцепления остается высоким в течение всего периода торможения.
АБС уменьшает износ шин, позволяет повысить поперечную устойчивость автомобиля и обеспечивает самый короткий тормозной путь.
Основными элементами этой системы являются датчики, контролирующие частоту вращения колес. Они передают импульсы на электронный блок управления для определения скорости вращения каждого колеса. Блок управления сравнивает скорости вращения колес и определяет, которое из них может быть заблокировано. Управляет тормозной системой гидравлический модулятор, имеющий электромагнитные клапаны, насос и реле управления клапанами и насосом.
Если появляется опасность блокировки колес, то электромагнитные клапаны перекрывают каналы поступления тормозной жидкости таким образом, чтобы блокировать повышение давления в гидравлических цилиндрах даже при нажатии водителем тормозной педали. При сохранении тенденции какого-либо из колес к блокировке, АБС откроет выпускной клапан для резкого сброса давления в системе этого колеса.
Скорость вращения колеса при этом станет расти, и как только ее значение превысит предельное значение, начнет повышаться давление тормозной жидкости и возобновится торможение. Эти циклы продолжаются в течение всего процесса автомобиля.
АБС работает при скорости движения автомобиля более 5 км/час и включенном зажигании. Напряжение в аккумуляторной батарее должно быть в норме. Если оно упало ниже 11 вольт или зажигание выключено, то АБС отключается и тормозная система работает в обычном режиме.
Видео «Недостатки АБС» - 3 мин.
8.2.5. Стояночная тормозная система
Стояночная тормозная система предназначена для удержания автомобиля на месте длительное время.
Стояночный тормоз (обиходное название – ручник) служит для удержания автомобиля на месте длительное время. Используется во время стоянки автомобиля, остановке на площадках с уклоном, а также в движении для осуществления резких поворотов на заднеприводных спортивных автомобилях. Стояночная тормозная система является также запасной (аварийной) системой, так как полностью дублирует гидравлическую рабочую систему. Применение стояночного тормоза в экстренном случае во время движения позволяет довести транспортное средство до полной остановки.
Как любая тормозная система стояночный тормоз состоит из тормозного привода и тормозных механизмов.
В стояночной тормозной системе используется в основном механический тормозной привод, который обеспечивает передачу тормозного усилия от человека к тормозному механизму.
Рис. 8.27 Механический привод стояночной тормозной системы
Самым популярным устройством является ручной рычаг, который располагается, как правило, справа от водителя рядом с сиденьем. Ручной рычаг оснащен храповым механизмом, обеспечивающим фиксацию стояночного тормоза в рабочем положении. На рычаге расположен выключатель контрольной лампы стояночного тормоза. Сама лампа установлена на панели приборов и включается при срабатывании стояночного тормоза.
От рычага к тормозным механизмам усилие передается с помощью тросов. В конструкции тормозного привода стояночного тормоза используются один, два или три троса. Самая популярная схема с тремя тросами: один передний (центральный) и два задних троса. Передний трос соединен с ручным рычагом, задние тросы – с тормозными механизмами. Для соединения переднего троса с задними тросами и равномерной передачи усилия используется т.н. уравнитель.
Непосредственное соединение тросов с элементами стояночного тормоза осуществляется с помощью наконечников, часть из которых регулируемые. Регулировочные гайки на концах тросов позволяют изменять длину привода. Возвращение системы в исходное положение (снятие с тормоза) производится при переводе ручного рычага в соответствующее положение с помощью возвратной пружины. Пружина может располагаться на переднем тросе, уравнителе или непосредственно на тормозном механизме.
Тормозной привод стояночной тормозной системы должен регулярно использоваться, в противном случае может произойти закисание тросов и потеря функций. Это особенно актуально для автомобилей с автоматической коробкой передач, где в силу конструкции коробки стояночным тормозом можно не пользоваться.
На некоторых современных легковых автомобилях применяется электрический привод стояночного тормоза, в котором электродвигатель непосредственно взаимодействует с дисковым тормозным механизмом. Система носит название электромеханический стояночный тормоз.
В конструкции стояночного тормоза используются, как правило, штатные тормозные механизмы задних колес, в которые внесены ряд изменений.
8.2.6. Тормозная система грузовых автомобилей большой грузоподъемности.
На большегрузных грузовых автомобилях и больших автобусах применяют тормозную систему с пневматическим приводом. Он позволяет получать достаточно большие силы в тормозных механизмах при небольших силах, прикладываемых водителем к тормозной педали.
В пневматический привод автомобиля входят компрессор 7, нагнетающий сжатый воздух в баллоны (ресиверы) 3, тормозные камеры 4, кран 7 управления, связанный тягой с тормозной педалью 3, и соединительная головка 5 с разобщительным краном, позволяющая присоединять тормозную систему прицепа к системе пневматического привода тормозов автомобиля-тягача. Рис. 8.28 Схема пневмопривода тормозов 1 - компрессор; 2 - манометр; 3 - баллоны для сжатого воздуха; 4 и 9 - тормозные камеры; 5и 6 - соединительная головка с разобщительным краном; 7 - трубопровод; 7 - тормозной кран (кран управления);
Вал компрессора приводится во вращение от коленчатого вала двигателя ременной передачей. Создаваемое компрессором давление, достигающее 0,65 - 0,8 МПа, автоматически ограничивается регулятором давления. Величину давления контролируют по манометру. Компрессор имеет общие с двигателем системы охлаждения и смазки.
Рис. 8.29 Схема компрессора
Система пневматического привода действует следующим образом: при нажатии педали кран управления сообщает тормозные камеры всех колес с ресиверами. Поступающий в каждую камеру сжатый воздух выгибает диафрагму, которая, действуя через шток, повертывает рычаг, а вместе с ним вал разжимного кулака тормозного механизма колеса, прижимающего колодки к тормозному барабану.
Рис. 8.30 Тормозной механизм
После отпускания педали кран управления разобщает с ресиверами тормозные камеры и соединяет их с атмосферой. Воздух из камер выходит, пружины, возвращают диафрагму в первоначальное положение, и торможение прекращается. Вмонтированные в рычаг червяк и червячная шестерня позволяют поворачивать вал относительно рычага и этим регулировать зазор между колодками и барабаном тормозного механизма.
8.2.7. Стояночная тормозная система грузовых автомобилей большой грузоподъемности
Стояночная тормозная система должна обеспечивать неподвижность автомобиля-тягача без прицепа на уклонах до 20%, автопоезда на уклонах до 18% и автопоезда только тормозной системой автомобиля-тягача на уклонах до 12%.
На протяжении многих лет стояночная тормозная система грузовых автомобилей ЗИЛ представляла собой трансмиссионный (центральный) тормозной механизм с ручным механическим приводом.
Рис. 8.31. Стояночный центральный тормоз:
1 -коробка передач; 2 - колодки; 3 - щиток; 4 - ось колодки; 5 - накладка; 6 - малая оттяжная пружина; 7 - кронштейн; 8 - болт; 9 - ограничительная шайба; 10 - фланец ведомого вала; 11 - гайка; 12 - большая оттяжная пружина; 13 - разжимной кулак; 14 - сухарь колодки; 15 - сальник; 16 - палец штанги; 17 - регулировочный рычаг; 18 - штанга; 19 - барабан тормоза; 20 - угловой рычаг; 21 - кронштейн углового рычага; 22 - тяга привода; 23 - вилка тяги; 24 - палец; 25 - ушко тяги; 26 - зубчатый сектор рычага привода; 27 - стопорная защелка; 28 - тяга стояночного привода тормозного крапа; 29 - тяга защелки; 30 - рычаг привода; 31 - рукоятка тяги защелки
Стояночный тормоз (рис. 8.31) имеет две симметричные колодки 2 с прикрепленными к ним фрикционными накладками и сухарями 14, которые шарнирно опираются на одну опорную ось 4, закрепленную в кронштейне 7 тормоза. В средней части колодки опираются бобышками на выступы кронштейна и удерживаются от боковых смещений шайбами, установленными на втулках и зажатыми болтами. Оттяжные пружины 6 и 12 возвращают колодки в отторможенное положение, прижимая их к разжимному кулаку и оси 4. На разжимном кулаке установлен регулировочный рычаг 17, к которому присоединяется тяга привода стояночного тормоза. Барабан 19 стояночного тормоза с фланцем насажен на шлицевой конец вала коробки передач и закреплен гайкой 11.
Для предохранения тормоза от попадания в него масла в кронштейне установлен сальник 15, а на фланце 10 - маслоотражатель, который сбрасывает просочившееся масло через специальное отверстие в кронштейне наружу. Щиток 3 тормоза, прикрепленный к кронштейну, защищает механизм от попадания в него грязи.
8.2.7.1. Стояночный тормоз прицепа
Стояночный тормоз (рис.8.32) имеет механический привод. Рукоятка привода у всех прицепов и полуприцепов по условиям безопасности должна располагаться на прицепе с левой стороны.
При вращении рукоятки I привода стояночного тормоза гайка 3, перемещаясь по винту 2, вдвигает кронштейн 5 в корпус 4 механизма привода, в результате чего происходит натяжение каната 9, который через блок 10 передает усилие на балансир 8, рычаг 7 и промежуточный вал II. Далее через рычаг 12 и серьгу 13 усилие перемещает регулировочный рычаг 6, который вызывает поворот разжимного кулака, разжимает тормозные колодки, вызывая торможение.
Рис. 8.32 Привод стояночного тормоза прицепа
8.2.8. Многоконтурный тормозной привод (МТП)
Высокую надежность тормозной системы обеспечивает МТП, который имеет более сложное, по сравнению с рассмотренным ранее устройством, применяется на большегрузных автомобилях и автобусах и включает в себя 5 независимых контуров пневмопривода тормозов.
Рис. 8.33
Помимо рабочей и стояночной автомобиль оборудован вспомогательной и запасной тормозной системами.
Вспомогательная тормозная система служит для длительного поддержания постоянной скорости (на затяжных спусках) за счет торможения двигателем. Это достигается прекращением подачи топлива в двигатель пневмоцилиндром и перекрытием выпускных трубопроводов пневмоцилиндром.
Запасная тормозная система служит для останова автомобиля при выходе из строя рабочей тормозной системы. При выпуске воздуха из рабочей тормозной системы срабатывают пружинные энергоаккумуляторы в тормозных камерах 15 среднего и заднего мостов (рис. 8.33)
Принципиальная схема действия тормозов следующая: сжатый воздух из компрессора 4 поступает в регулятор давления 5, который автоматически поддерживает давление сжатого воздуха в пневмоприводе. Из регулятора давления воздух поступает в предохранитель 6 от замерзания конденсата. Воздух, проходящий через предохранитель, насыщается парами специальной жидкость, которые препятствуют замерзанию конденсата. Далее воздух поступает к двойному 7 и тройному 10 защитным клапанам, к которым присоединены пневмоприводы следующих 5 независимых контуров:
Первый контур привода тормозных механизмов передних колес (воздушный баллон 16 – трубопроводы – нижняя секция тормозного крана 18 – клапан 19 ограничения давления – тормозные камеры 21 передних колес).
Тормозной кран распределяет воздух по контурам. Количество секций крана соответствует числу контуров.
Второй контур привода приводных механизмов среднего и заднего мостов (воздушный баллон 8 – трубопроводы – верхняя секция тормозного крана – автоматический регулятор 13 тормозных сил – тормозные камеры 15 среднего и заднего мостов с пружинными энергоаккумуляторами)
Третий контур привода механизмов стояночной и запасной тормозных систем прицепа (воздушные баллоны 14 – тормозной кран 2 обратного действия с ручным управлением стояночным тормозом – ускорительный клапан 11 – двух магистральный клапан 12 – цилиндры с пружинными энергоаккумуляторами, объединенными с тормозными камерами среднего и заднего мостов)
Четвертый контур привода механизма вспомогательной тормозной системы и питания потребителей сжатого воздуха в автомобиле (пневматический кран 20 управления – цилиндры привода заслонок выпускных трубопроводов – цилиндр выключения подачи топлива)
Пятый контур системы пневматического аварийного растормаживания стояночного тормоза (кран 1 аварийного растормаживания, подключенный к тройному защитному клапану 10)
Давление в первом и втором контурах можно контролировать по двух стрелочному манометру на панели приборов в кабине автомобиля. Контроль за исправностью тормозных систем обеспечивается световой и звуковой сигнализацией, датчики которой - пневматические выключатели – расположены в разных точках системы пневмопривода.
Тормозные камеры передних колес автомобилей большой грузоподъемности подобны тормозным камерам автомобиля общего назначения (см. рис. 8.30). Тормозные камеры средних и задних колес выполнены совместно с пружинными энергоаккумуляторами. Они предназначены для приведения в действие тормозных механизмов задних колес при включении рабочей, стояночной и запасной или аварийной тормозных систем.
Рис. 8.34 Тормозная камера с пружинным энергоаккумуляром
Сама тормозная камера является составной частью второго контура пневмопривода рабочей тормозной системы, а энергоаккумулятор входит в третий контур привода механизмов стояночной и тормозной тормозных систем. Работа стояночной и запасной тормозных систем происходит при обратном действии, т.е. при подаче сжатого воздуха в энергоаккумулятор осуществляется растормаживание, а при выпуске воздуха – затормаживание колес.
Тормозная камера (рис. 8.34) с пружинным энергоаккумулятормом состоит из корпуса 9, фланца крышки 11 и цилиндра 14, соединенных вместе. Между корпусом и крышкой помещена диафрагма 10. Посредством опорного диска 5 диафрагма 10 соединена со штоком 8. В цилиндре 14 энергоаккумулятора установлен поршень 15, который под действием силовой пружины 1 перемещается вниз (относительно рисунка). Поршень жестко соединен с толкателем 4, который может перемещаться в крышке 11, действуя через подпятник 12 на диафрагму 10. Полости А и В соединены между собой трубкой 3 и через отверстие Д сообщаются в атмосферой.
На рис. 8.34 положение деталей показано во время движения автомобиля, т.е. в расторможенном состоянии. При этом сжатый воздух их воздушного баллона через отверстие Е подводится в полость Б цилиндра под поршень. Поршень находится в верхнем положении (показано на рис.), а силовая пружина 1 полностью сжата. Диафрагма под действием возвратной пружина 7 прогнулась вверх, переместив толкатель вслед за поршнем.
Когда нажатием на педаль тормоза включают в действие рабочую тормозную систему, сжатый воздух подается через отверстие Д в полость на диафрагмой. Диафрагма прогибается вниз и через шток 8 перемещает рычаг тормозного механизма (см. рис. 8.30). Происходит торможение автомобиля. При этом давление в полости Б через отверстие Е не изменяется, и пружина 1 остается сжатой.
Во время включения стояночной или запасной тормозной систем сжатый воздух выпускается из полости Б через отверстие Е, и силовая пружина разжимается, действуя через поршень, толкатель и диафрагму на шток 8. Шток перемещает рычаг тормозного механизма, и автомобиль затормаживается. Стояночный тормоз включают только после полного останова автомобиля.
При включении стояночной и запасной тормозных систем сжатый воздух подается в цилиндр энергоаккумулятора под поршень через отверстие Е. Поршень, поднимаясь, сжимает силовую пружину 1. Одновременно с поршнем поднимается толкатель 4, освобождая диафрагму 10. Под действием возвратной пружины 7, диафрагма и шток занимают начальное положение.
Лекция 14. Рулевое управление.
Назначение рулевого управления.
Рулевое управление обеспечивает необходимое направление движения автомобиля. Рулевое управление включает рулевой механизм, который осуществляет передачу усилия от водителя к рулевому приводу, и рулевой привод, который осуществляет передачу усилия от рулевого механизма к управляемым колесам. Каждое управляемое колесо установлено на поворотной цапфе (поворотном кулаке) 13 (рис. 1), соединенной с балкой 11 моста шкворнем 8 . Шкворень неподвижно закреплен в балке, и его верхний и нижний концы входят в проушины поворотной цапфы. При повороте цапфы за рычаг 7 она вместе с установленным на ней управляемым колесом поворачивается вокруг шкворня. Поворотные цапфы соединены между собой рычагами 9 и 12 и поперечной тягой 10 . Поэтому управляемые колеса поворачиваются одновременно.
Рис. 1. Схема рулевого управления
Поворот управляемых колес осуществляется при вращении водителем рулевого колеса 1 . От него вращение передается через вал 2 на червяк 3 , находящийся в зацеплении с сектором 4 . На валу сектора закреплена сошка 5 , поворачивающая через продольную тягу 6 и рычаг 7 поворотные цапфы 13 с управляемыми колесами.
Рулевое колесо 1 , вал 2 , червяк 3 и сектор 4 образуют рулевой механизм, увеличивающий момент, прикладываемый водителем к рулевому колесу для поворота управляемых колес. Сошка 5 , продольная тяга 6 , рычаги 7 , 9 и 12 поворотных цапф и поперечная тяга 10 составляют рулевой привод, передающий усилие от сошки к поворотным цапфам обоих управляемых колес. Поперечная тяга 10 , рычаги 9 и 12 , балка 11образуют рулевую трапецию, обеспечивающую необходимое соотношение между углами поворота управляемых колес.
Управляемые колеса поворачиваются на ограниченный угол, равный, как правило, 28 - 35º. Это сделано для того, чтобы колеса при повороте не касались рамы, крыльев и других деталей автомобиля.
На некоторых автомобилях в рулевом управлении используют усилитель, облегчающий поворот управляемых колес.
Стабилизация управляемых колес.
Силы, действующие на автомобиль, стремятся отклонить управляемые колеса от положения, соответствующего прямолинейному движению. Чтобы препятствовать повороту колес под действием случайных сил (толчков от наезда на неровности дороги, порывов ветра и т.п.), управляемые колеса должны сохранять положение, соответствующее прямолинейному движению, и возвращаться в него из любого другого положения. Эта способность называется стабилизацией управляемых колес. Стабилизация колес обеспечивается наклонами шкворня в поперечной и продольной плоскостях
и упругими свойствами пневматической шины.
Конструкция рулевых механизмов.
Червячно-роликовый рулевой механизм , показанный на рис. 2, выполнен в виде глобоидного червяка 5 и находящемся с ним в зацеплении трехгребневого ролика 8 . Червяк установлен в чугунном картере 4 на двух конических роликовых подшипниках 6 . Беговые дорожки для роликов обоих подшипников сделаны непосредственно на червяке. Наружное кольцо верхнего подшипника запрессовано в гнездо картера. Наружное кольцо нижнего подшипника, установленного в гнезде картера со скользящей посадкой, опирается на крышку 2 , привернутую к картеру болтами. Под фланцами крышки поставлены прокладки 3 различной толщины для регулирования предварительного натяга подшипников.
Червяк имеет шлицы, которыми он напрессован на вал. В месте выхода вала из картера установлен сальник. Верхняя часть вала, имеющая лыску, входит в отверстие фланца вилки карданного шарнира 7 , где закрепляется клином. Через карданный шарнир рулевая пара связана с рулевым колесом.
Вал 9 сошки установлен в картер через окно в боковой стенке и закрыт крышкой 14 . Опорой вала служат две втулки, запрессованные в картер и крышку. Трехгребневый ролик 8 размещен в пазу головки вала сошки на оси с помощью двух роликовых подшипников. С обеих сторон ролика на его ось поставлены стальные полированные шайбы. При перемещении вала сошки изменяется расстояние между осями ролика и червяка, чем обеспечивается возможность регулирования зазора в зацеплении.
Рис. 2. Рулевой механизм автомобиля КАЗ-608 «Колхида»
На конце вала 9 нарезаны конические шлицы, на которых гайкой закреплена рулевая сошка 1 . Выход вала из картера уплотнен сальником. На другом конце вала рулевой сошки имеется кольцевой паз, в который плотно входит упорная шайба 12 . Между шайбой и торцом крышки 14 находятся прокладки 13 , используемые для регулирования зацепления ролика с червяком. Упорную шайбу с комплектом регулировочных прокладок закрепляют на крышке картера гайкой 11 . Положение гайки фиксируют стопором 10 , привернутым к крышке болтами.
Зазор в зацеплении рулевой передачи переменный: минимальный при нахождении ролика в средней части червяка и увеличивающийся по мере поворота рулевого колеса в ту или другую сторону.
Такой характер изменения зазора в новой рулевой передаче обеспечивает возможность неоднократного восстановления необходимого зазора в средней, наиболее подверженной изнашиванию зоне червяка без опасности заедания на краях червяка. Подобные рулевые механизмы используются на автомобилях ГАЗ, ВАЗ с разницей в механизме регулировки зацепления червяка 5 с роликом 8 .
Реечный рулевой механизм (рис. 3, а ). При повороте рулевого колеса 1 шестерня 2 перемещает рейку 3 , от которой усилие передается на рулевые тяги 5 . Рулевые тяги за поворотные рычаги 4 поворачивают управляемые колеса. Реечный рулевой механизм состоит из косозубой шестерни 2 , нарезанной на валу 8 (рис. 3, б ) и косозубой рейки 3 . Вал вращается в картере 6 на упорных подшипниках 10 и 14 , натяг которых осуществляется кольцом 9 и верхней крышкой 7 . Упор 13 , прижатый пружиной 12 к рейке, воспринимает радиальные усилия, действующие на рейку, и передает их на боковую крышку 11 , чем достигается точность зацепления пары.
Рис. 3. Рулевое управление с реечным механизмом:
а – схема рулевого управления; б – реечный рулевой механизм
Винтореечный рулвой механизм (рис. 4) имеет две рабочие пары: винт 1 с гайкой 2 на циркулирующих шариках 4 и поршень-рейку 11 , входящую в зацепление с зубчатым сектором 10 вала сошки. Передаточное отношение рулевого механизма 20:1. Винт 1 рулевого механизма имеет шлифованную с большой точностью винтовую канавку «арочного» профиля. Такая же канавка выполнена в гайке 2 . Винтовой канал, образованный винтом и гайкой, заполнен шариками. Гайка жестко закреплена внутри поршня-рейки стопором.
Рис. 4. Рулевой механизм с встроенным гидроусилителем:
а – устройство; б – схема работы; 1 – винт; 2 – гайка; 3 – желоб; 4 – шарик; 5 – рулевой вал;
6 – корпус клапана управления; 7 – золотник; 8 – сошка; 9 – вал сошки; 10 – зубчатый сектор; 11 – поршень-рейка; 12 – картер-цилиндр; 13 – картер; А и Б – полости цилиндра;
В и Г – шланги входа и выхода масла; Д и Е – каналы.
При вращении винта 1 от рулевого колеса, шарики выходят с одной стороны гайки в желоб 3 и возвращаются по нему в канавки винта с другой стороны гайки.
Зубчатая рейка и зубчатый сектор имеют переменные по толщине зубья, что позволяет регулировать зазор в зацеплении рейка-сектор регулировочным винтом, ввернутым в боковую крышку картера рулевого механизма. На поршне-рейке установлены упругие разрезные чугунные кольца, обеспечивающие его плотную посадку в картере-цилиндре 12 . Вращение рулевого вала преобразуется в поступательное движение поршня-рейки благодаря перемещению гайки по винту. Зубья поршня-рейки в результате поворачивают сектор, а вместе с ним и вал 9 с сошкой 8 . Перед картером рулевого механизма в корпусе 6 установлен клапан управления с золотником 7 . С клапаном управления шлангами В и Г соединен насос гидроусилителя.
Во время движения автомобиля по прямой золотник находится в среднем положении (как показано на рис. 4), и масло из насоса по шлангу Г через клапан управления перекачивается обратно в бачок по шлангу В . При повороте рулевого колеса влево золотник 7 перемещается вперед (на рисунке влево) и открывает доступ масла в полость А по каналу Д , а из полости Б масло идет в полость В и в насос. В результате чего облегчается поворот колеса влево. Если водитель приостановит вращение рулевого колеса, то золотник клапана управления займет среднее положение, и угол, на который повернуты направляющие колеса, останется неизменным.
При повороте рулевого колеса вправо винт с золотником 7 перемещается назад (на рисунке вправо) в результате взаимодействия зубьев поршня-рейки и сектора. Перемещаясь назад, золотник открывает доступ маслу в полость Б через канал Е . В результате давления масла на поршень-рейку уменьшается усилие, которое затрачивается на поворот рулевого колеса. При этом рулевая сошка поворачивается против хода часовой стрелки.
Рулевой привод.
Рулевая трапеция (рис. 5). В зависимости от компоновочных возможностей рулевую трапецию располагают перед передней осью (передняя рулевая трапеция) или за ней (задняя рулевая трапеция). При зависимой подвеске колес применяют трапеции с цельной поперечной тягой; при независимой подвеске – только трапеции с расчлененной поперечной тягой, что необходимо для предотвращения самопроизвольного поворота управляемых колес при колебаниях автомобиля на подвеске. С этой целью шарниры разрезной поперечной тяги должны располагаться так, чтобы колебания автомобиля не вызывали их поворота относительно шкворней. Схемы различных рулевых трапеций показаны на рис. 9.
Рис. 5. Схемы рулевых трапеций
При зависимой и независимой подвесках могут применяться как задняя (рис. 9, а ), так и передняя (рис. 9, б ) трапеции.
На рис. 9, в – е приведены задние трапеции независимых подвесок с разным числом шарниров.
Конструкция рулевых приводов при зависимой подвеске. При повороте колес детали рулевого привода перемещаются одна относительно другой. Такое перемещение происходит также при наезде колеса на неровности дороги и при колебаниях кузова относительно колес. Для создания возможности относительного перемещения деталей привода в горизонтальной и вертикальной плоскостях при одновременной надежной передаче усилий соединение осуществляют в большинстве случаев шаровыми шарнирами.
Продольную тягу 1 (рис. 6, а ) рулевого привода делают трубчатой с утолщениями по краям для монтажа деталей двух шарниров. Каждый шарнир состоит из пальца 3 , сухарей 4 и 7 , охватывающих сферическими поверхностями шаровую головку пальца, пружины 8 и ограничителя 9 . При затягивании пробки 5 головка пальца зажимается сухарями, а пружина 8 сжимается. Пружина шарнира не допускает образования зазоров в результате износов и смягчает толчки, передаваемые от колес на рулевой механизм. Ограничитель предотвращает чрезмерное сжатие пружины, а при ее поломках не позволяет пальцу выйти из соединения с тягой. Пружины располагают в тяге относительно пальцев 2 и 3 так, чтобы через пружины передавались усилия, действующие на тягу как от сошки 6 , так и от поворотного рычага.
![]() |
Рис. 6. Рулевые тяги автомобиля ГАЗ:
а – продольная; б – поперечная
В поперечной продольной тяге шарниры размещают в наконечниках, навинченных на концы тяги. Резьба на концах тяги обычно имеет резное направление. Поэтому вращением тяги 10 (рис. 6, б ) при неподвижных наконечниках 11 можно изменять ее длину при регулировании схождении колес. Пальцы 15 жестко закрепляют в рычагах поворотных цапф. Шаровой поверхностью палец прижимается предварительно сжатой пружиной 12 через пятку 13 к сухарю 14 , установленному внутри наконечника тяги. Такое устройство шарнира позволяет непосредственно передавать усилия от пальца на тягу и в обратном направлении. Пружина 12 обеспечивает устранение в шарнире зазора, обусловленного износом. Таким образом, основное отличие шарниров поперечной тяги от шарниров продольной тяги состоит в том, что в первых не имеется пружин, через которые непосредственно передаются усилия в рулевом приводе.
Шарниры рулевых тяг смазывают через масленки. На некоторых автомобилях в шарниры смазочный материал закладывают при сборке, и пополнять ее в процессе эксплуатации не требуется.
Особенности рулевых приводов при независимой подвеске управляемых колес (рис. 7) . Рулевой привод при независимой подвеске должен исключать произвольный поворот каждого колеса в отдельности при его качании на подвеске. Для этого необходимо возможно близкое совпадение осей качания колеса и тяги привода, что достигается применением разрезной поперечной тяги. Такая тяга состоит из шарнирно соединенных частей, которые перемещаются с колесами независимо одна от другой.
Рис. 7. Схема рулевого привода при независимой подвеске:
1 – стойка; 2 – поворотные цапфы; 3 – рычаг поворотной цапфы; 4 и 9 – боковые тяги;
5 – маятниковый рычаг; 6 – сошка; 7 – рулевой механизм; 8 – средняя тяга.
Важнейшей частью рулевого управления любого автомобиля является рулевой механизм, который мы сокращённо будем называть РМ. В качестве его главной функции выступает увеличение прикладываемого к автомобильному рулю усилия, а также его передача к рулевому приводу. С точки зрения механики этот процесс выглядит как преобразование вращательных движений руля в поступательные движения рулевых тяг.
Для обеспечения бесперебойности и точности протекания данного процесса, современный РМ должен отвечать следующим требованиям:
- обладать высокой степенью надежности;
- иметь незначительные по размерам технологические зазоры для обеспечения свободного вращения рулевого колеса;
- обладать возможностью произвольного возврата руля в нейтральное положение после прекращения действия на него мускульного усилия рук водителя;
- иметь оптимальное передаточное число, которое определяет отношение между углом поворота руля и усилия, прикладываемого к нему.
Устройство рулевого механизма
Рулевой механизм (РМ) имеет довольно сложное устройство, а самой главной его частью является редуктор, состоящий из зубчатых колес. В зависимости от марки и модели автомобиля редуктор может быть заключен в корпус из сварной высокопрочной стали или литого чугуна. Помимо зубчатых колес в нем размещаются и другие элементы: подшипники, валы. В некоторых разновидностях редукторов внутри корпуса могут быть размещены и устройства для автономной смазки зацеплений и подшипников.
Разновидностей редукторов в наши дни довольно много. Следует привести некоторые из них с учетом критерия классификации:
- тип передачи – «червячные» и зубчатые
- форма зубчатых колес – конические, цилиндрические и коническо-цилиндрические;
- расположение валов – горизонтальные и вертикальные;
- особенность кинематической схемы – раздвоенная ступень и развернутая соосная схема;
- число ступеней – одно- и двухступенчатые.
Типы рулевых механизмов:
- Реечный РМ
Наиболее распространенным в наше время типом РМ является реечный. Причина такой популярности кроется в относительной простоте конструкции, его небольшой массе, низкой себестоимости производства, высоком КПД и небольшом числе шарниров и тяг, что значительно уменьшает частоту поломок. Кроме этого, расположение этого типа рулевого механизма поперек корпуса авто освобождает место в подкапотном пространстве для размещения в нем других механизмов и узлов, например, трансмиссии, двигателя и т.д. Реечное управление является довольно жестким, поэтому обеспечивает довольно высокую маневренность автомобиля.
Обладает реечный механизм и рядом недостатков. Среди них наиболее серьезными являются:
- сложность технологии установки на авто, имеющих зависимую подвеску управляемых колес;
- высокая виброактивность рулевого управления;
- повышенная восприимчивость к ударам подвески.
Состоит реечный рулевой механизм из вкладыша, чехла, пружин, шарового пальца, шарового шарнира, упоров, шестерен и непосредственно самой рулевой рейки. Реечные шестерни располагаются в трубке из металла, с каждой стороны которой выступает сама рейка. Рулевой наконечник соединен с каждой из ее сторон. Ведущая же шестерня рулевого механизма сопряжена с валом рулевой колонки, который при вращении руля также начинает поворачиваться, и приводит тем самым в движение рейку.
На легковые автомашины, имеющие зависимую подвеску управляемых колес, а также малотоннажные грузовики и автобусы, автомобили с повышенной проходимостью устанавливают другой тип рулевого механизма – «червячный». Современный его вариант состоит из ролика, «червяка», который имеет переменный диаметр (его еще называют глобоидным «червяком») и соединенный с рулевым валом. Вне корпуса механизма находится рычаг (сошка), который соединен с тягами рулевого привода. Во время вращения руля происходит катание ролика по «червяку» и качание рычага (сошки), что приводит в движение управляемые колеса.
Главными отличиями «червячного» механизма от реечного выступают его меньшая чувствительность к ударам подвески и большие максимальные углы поворота колес. Недостатками же такого механизма являются его дороговизна изготовления и необходимость в постоянной регулировке.
На многотоннажных грузовых автомобилях, больших автобусах и некоторых легковых автомашинах представительского класса используется винтовой рулевой механизм. Он состоит из таких конструктивных элементов:
- винта, который располагается на рулевом валу;
- гайки, перемещающейся по валу;
- зубчатой рейки, которая нарезана на гайке;
- зубчатого сектора, соединенного с рейкой;
- рулевой сошки, которая располагается на валу сектора.
Главной же особенностью механизма является соединение винта и гайки при помощи шариков, что ведет к серьезному уменьшению трения и износа. Сам принцип работы во многом похож на принцип работы «червячного» рулевого механизма. Во время вращения руля происходит поворот рулевого вала и винта, расположенного на нем, который приводит в движение гайку, все это сопровождается циркуляцией шариков. Гайка же через зубчатую рейку сдвигает зубчатый сектор, а с ним и рулевую сошку.
Винтовой рулевой механизм обладает высоким КПД и может передавать большие усилия.
Как проверить работоспособность РМ?
Как и в случае с другими элементами рулевого управления регулярная проверка работоспособности рулевого механизма является важнейшей задачей каждого автовладельца, ведь от этого самым непосредственным образом будет зависеть безопасность передвижения на автомобиле.
В первую очередь, следует проверять люфт рулевого колеса. Проверка производится как вручную, так и с применением специального прибора – динамометра-люфтометра. Его нужно закрепить на ободе колеса и приложить силу, равную 10 Н. Надо произвести замеры зазоров в шарнирах рулевых тяг и «червячных» подшипниках. В том случае, если автомобиль оборудован усилителем руля (так называемом ГУР), то такая проверка должна производиться при работающем моторе.
Визуальный осмотр также является важной составляющей диагностики работоспособности РМ. В его ходе нужно особое внимание уделить состоянию защитных чехлов шаровых шарниров, так как через трещины в них в рулевой механизм проникает грязь, что может привести к его некорректной работе, поломке и даже разрушению. При малейших сомнениях в надлежащей работе РМ необходимо обратиться в специализированный автосервис.
Как снять рулевой механизм и как его установить?
Процесс снятия и установки рулевого механизма рассмотрим на примере ВАЗ 2106, на котором применяется «червячный» тип. Для этого понадобится следующий инструмент:
- 2 ключа «на 13»;
- ключ «на 22»;
- плоскогубцы;
- съемник пальцев шаровых.
Сам процесс снятия механизма будет следующим:
- Первым шагом требуется снять рулевой вал.
- После этого отсоединить левую боковую и среднюю рулевые тяги и отвести их по сторонам.
- Далее, одним ключом «на 13» придерживая болты крепления рулевого механизма от проворачивания, вторым отвернуть гайки и снять их вместе с шайбами.
- После чего, придерживая механизм рукой, надо вынуть болты крепления, оставив при этом рулевой механизм лежать на лонжероне.
- Вытащить его через подкапотное пространство.
Новый РМ устанавливается в обратном порядке, но с учетом некоторых нюансов: не следует плотно затягивать болты крепления кронштейна рулевого вала и гайки на компенсаторе, а также болты крепления картера рулевого механизма к лонжеронам. Это делается с той целью, чтобы установить новый механизм в правильное положение.
Производится это с помощью двух- или трехкратного вращения рулевого колеса в разные стороны, при этом произойдет самоустановка механизма и рулевого вала.
После этого можно приступать к контрольному затягиванию всех элементов крепления. Финишным же этапом будет проверка наличия масла в рулевом механизме автомобиля.
После этого необходимо произвести регулировку механизма.
Регулировка рулевого механизма
Самый популярный тип рулевого механизма (реечный) время от времени нуждается в регулировке. Причиной этого, как уже упоминалось выше, является высокая восприимчивость механизма к кочкам, ямам и ухабам, которых на наших дорогах довольно много. На большинстве моделей современных автомобилей регулировку рейки можно сделать своими силами.
Процесс регулировки осуществляется с помощью регулировочного винта, который, чаще всего, располагается на торцевой крышке РМ. Для облегчения доступа к нему лучше воспользоваться смотровой ямой, эстакадой или подъемником, в противном же случае придется немного полежать на земле. Если регулировка производится на домкратах, то перед подъемом следует выставить передние колеса в ровном положении.
После проведения подготовительных мероприятий надо замерить люфт, максимальный показатель которого не должен превышать 10 градусов. Далее требуется произвести подтяжку регулировочного винта, причем делать это необходимо плавно и медленно, все время контролируя люфт с помощью динамометра-люфтометра. После завершения регулировки следует проверить ход рулевого колеса в движении, и если он слишком тугой, то необходимо немного ослабить регулировочный винт.
Как самостоятельно починить рулевой механизм?
Некоторые неисправности в РМ можно устранить, не прибегая к его замене. О некоторых способах пойдет речь далее. Если наблюдается течь, то это может свидетельствовать об отсутствии герметичности в соединениях трубок цилиндра или неисправности сальника, а также коррозии вала редуктора. Для устранения данной неисправности необходимо произвести полную переборку агрегата. Если причина в сальниках и прокладках, то необходимо их заменить на новые, а если дело заключается в серьезной коррозии вала, то его следует отшлифовать и при помощи газотермонапыления восстановить до исходных размеров.
Сильный люфт может указывать на выход из строя и износ таких деталей РМ как, например, картер, шарниры или подшипник винта. Причиной люфта может быть и кривой картер или вал. Чтобы устранить эту неисправность, нужна, опять-таки, полная переборка узла, в ходе которой потребуется замена изношенных деталей.
Сильный стук в редукторе РМ говорит обычно об износе ударных подшипников. То есть потребуется их замена на новые. Но это может быть свидетельством и такой неисправности как искривление вала или серьезный износ шарниров. Для более точной диагностики может вновь потребоваться полная переборка узла.
Средние цены на ремонт РМ в России и СНГ
Однако на устранение неполадок в рулевом механизме не всегда есть свободное время, да и многие из ремонтных операций требуют наличия довольно серьезных навыков в автослесарном деле, поэтому обращение к услугам специалистов в автосервисы видится правильным выбором.
Конечная стоимость сервисных работ будет зависеть не только от серьезности поломки, но также и марки/модели автомобиля, срочности и некоторых других факторов. В среднем же, стоимость (без учета стоимости заменяемых элементов) некоторых работ, связанных с обслуживанием рулевых механизмов, в автомастерских России и стран ближнего зарубежья в перерасчете на рубли такова:
- замена рулевого механизма, имеющего усилитель руля – от 700 рублей;
- замена силового цилиндра – от 500 рублей;
- ремонт силового цилиндра – от 300 рублей;
- замена рулевых наконечников – от 400 рублей;
- замена пальцев вкладыша – от 100 рублей;
- замена рулевой рейки – от 2 000 рублей;
- регулировка рулевой рейки – от 200 рублей;
- ремонт рулевой рейки без снятия механизма с авто – от 1000 рублей;
- замена рулевой трапеции – от 1 000 рублей;
- замена пыльников рулевого механизма – от 1 800 рублей.
Средние цены на новые РМ в России и странах СНГ
Иногда производить ремонт рулевого механизма нецелесообразно, а иногда и просто невозможно, например, после серьезного ДТП, поэтому может потребоваться приобретение нового узла на замену старому. Естественно, что стоимость нового рулевого механизма зависит не только от его типа, но и марки и модели автомобиля, оригинальности самого механизма, ведь на многие популярные модели авто крупными (и не очень) производителями запчастей выпускаются неоригинальные рулевые механизмы.
Средняя же стоимость на новые рулевые механизмы по России и странам ближнего зарубежья в перерасчете на отечественную валюту такова:
- на заднеприводные автомобили отечественного производства (ВАЗ 2105, 2107, 2106, ИЖ Ода) – от 2 000 рублей;
- на переднеприводные автомобили отечественного производства (ВАЗ 2109, 2114, Приора, Гранта, Калина, Largus) – от 2 500 рублей;
- на бюджетные автомобили иностранного производства (KIA Ria, Renault Logan, Toyota Corolla, Hyundai Accent (Solaris), Ford Fiesta,) – от 7 000 рублей;
- на автомобили иностранного производства бизнес-класса (Ford Mondeo, Toyota Camry, Volvo S40) – от 12 000 рублей;
- на автомобили иностранного производства премиум-класса (Mercedes S-classe, BMW 7, Audi A8) – от 22 000 рублей;
- на грузовые автомобили отечественного производства (КамАЗ, ГАЗ) – от 25 000 рублей.
Стоит добавить, что в связи с изменениями курсов основных иностранных валют, стоимость рулевых механизмов на автомобили иностранного производства может изменяться в большую или, как это ни странно, в меньшую сторону.